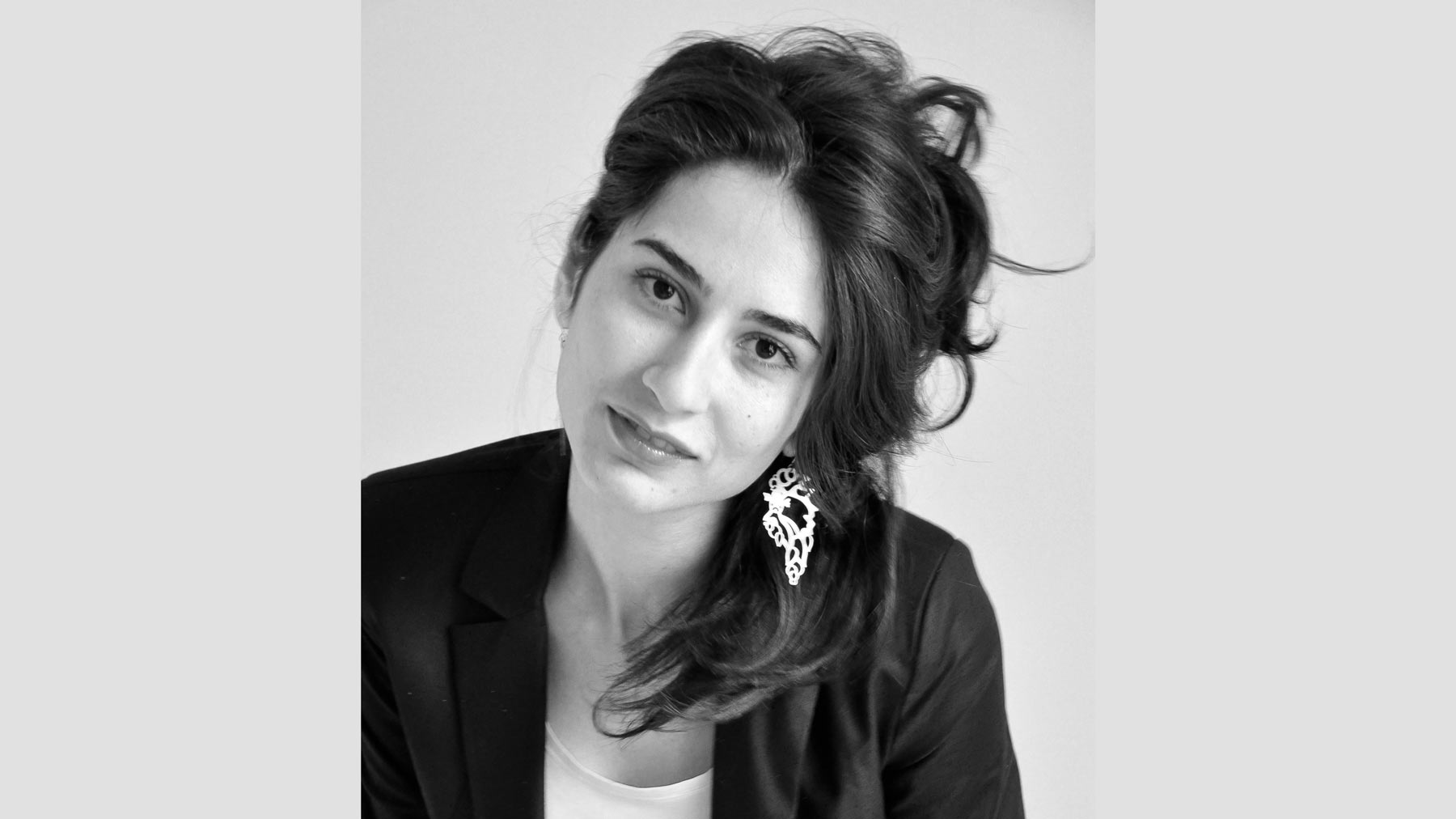
Meibodi: From Science Fiction to Reality in Concrete
From the slabs undergirding suburban tract homes to the inner cores of glass-clad skyscrapers, the modern built environment is founded on concrete — worldwide, some 10 billion tons of it every year. But in addition to being the most common building material, concrete is also the most polluting; along with the iron rebar used to give it form, its production is responsible for as much as 11 percent of global carbon dioxide emissions.
Concrete technology hasn’t changed much since ancient times — it’s still a mixture of lime-based cement, water, sand, and aggregates. But Mania Aghaei Meibodi, an assistant professor of architecture whose research involves 3D printing concrete formwork, is on the front lines of a revolution that will transform the construction industry and reduce concrete’s impact on the environment — all while freeing architects to realize designs that were previously unimaginable.
“First and foremost, it will allow any shape, with no restriction in terms of fabrication,” Meibodi says, noting that 3D printing can create lighter, more complex building parts, which use only as much concrete as is absolutely necessary. “You can reduce the overall weight of building if you reduce the weight of the wall or the façade. Then, eventually, even the foundation will be lighter because it has to carry less weight.”
Meibodi came to Taubman College in 2019 after a post-doctoral stint at ETH Zurich. There, she led the “Smart Slab” project for the DFAB House in Dübendorf, Switzerland — the world’s first full-scale building to use additive manufacturing for production of a lightweight slab with functional integration. Meibodi’s slab, its design optimized by computer software, used 3D-printed formwork and a combination of sprayed-on and cast fiber-reinforced concrete. Just 20 millimeters thick at most points, the undulating, organic-looking slab is less than half the weight of a conventional concrete slab yet still supports a two-story timber structure.
MinMax, a very thin, lightweight GRFC facade prototype with highly detailed surface, as exhibited at Swissbau. Meibodi built the structure in collaboration with Stahlton Bauteile AG. Photo credit: Girts Apskalns.
The internationally acclaimed project offers a high-end proof-of-concept for technology that Meibodi foresees filtering down to more vernacular architecture — and in fact, that’s already happening. A Chinese firm built a 3D-printed concrete villa in 2016, boasting that the imposing mansion was also earthquake-proof. In late 2019, the first 3D-printed neighborhood welcomed residents in an impoverished rural area of southern Mexico. Germany’s first 3D-printed residential building went up in the city of Beckum last fall. And while they offer new possibilities for speedy construction and enhanced creativity, 3D printing and computational design also will make a difference at less visible levels, in buildings that are not only more efficiently constructed but that also use less energy once they’re built.
“We can do so many things that we couldn’t do before, when we didn’t have the computing power we have now,” says Meibodi, who is now at work on a project to develop robotic 3D printing of thermoplastic formwork, a technique for casting concrete without heavy, rigid molds and scaffolding. She and her collaborators, who include Wes McGee, associate professor of architecture at Taubman College, and Victor Li, a professor in U-M’s College of Engineering, are constructing composite concrete walls, their freeform shapes unlimited by traditional building techniques.
“With this technology, you can create any geometry,” Meibodi says. “With geometry, building façades could really contribute to environmental factors — you can guide the wind around your building, guide the light inside it, or collect water. And if you think about all the systems that we add to a building — wires, pipes, ducts — these usually go on top of the structures. But with 3D printing, we can integrate them by printing voids with space for plumbing, HVAC, and electrical systems, with printed access points for fixing them. This is a new kind of building, a building that’s lighter, that’s thinner, and that also integrates systems.”
Meibodi was lured to Michigan in large part by the facilities that would be at her disposal here, especially Taubman College’s Digital Fabrication Lab (FABLab). “The University of Michigan is at the frontier of digital fabrication,” she says. “We have one of the best facilities in the world, and we’re now seeing other universities beginning to adopt the technologies we have.”
But the nearness of Detroit, a city with such potential for “rebirth,” as she puts it, also was a draw. “Detroit has the space and the infrastructure for these technologies,” she explains. “I envision that we will have many projects in Detroit.”
Detroit, after all, was at the heart of an earlier revolution in the way we conceive of the human environment. So it makes sense, she says, that it could play a part in the next one — a revolution that is already underway.
“Architecture has changed dramatically in the last 20 years,” she says. “When I started, I saw a lot of resistance to change. Now I don’t, because this is becoming reality. There is no more science fiction about it. We are building it. It’s out there.”
—Amy Crawford